Hydraulic fluid is a crucial component of hydraulic systems, which are used in a wide range of industries and applications. It is a non-compressible fluid that is responsible for transferring power within the hydraulic system. Hydraulic fluid is also used to lubricate moving parts, act as a coolant, and seal the system.
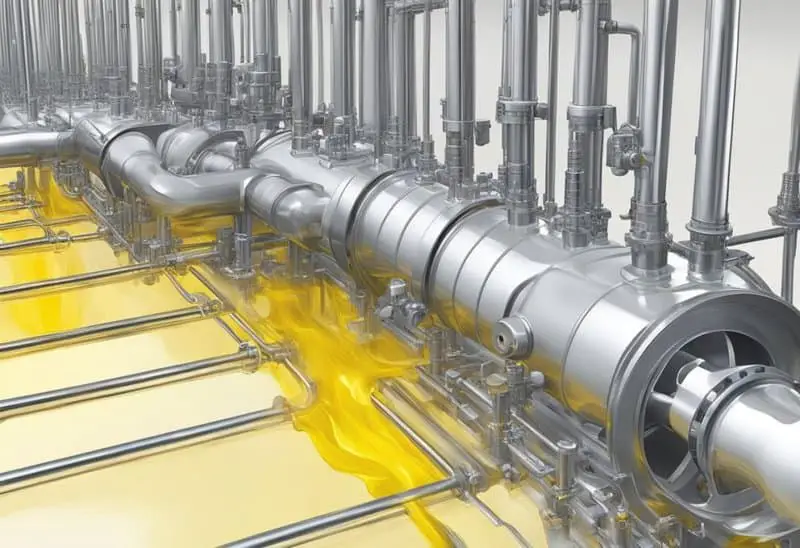
The composition of hydraulic fluid varies depending on the specific application and requirements of the hydraulic system. However, most hydraulic fluids are based on mineral oil or water. Synthetic-based hydraulic fluids are also available and are commonly used in applications where mineral oil-based fluids are not suitable.
The properties of hydraulic fluid are carefully selected to ensure optimal performance of the hydraulic system. These properties include viscosity, lubricity, thermal stability, and resistance to oxidation and corrosion. Understanding the composition and properties of hydraulic fluid is essential for maintaining and optimizing the performance of hydraulic systems.
Composition of Hydraulic Fluid
Hydraulic fluid is a non-compressible fluid that is used to transmit power between hydraulic machinery and equipment. It is a combination of base oil and various additives. The composition of hydraulic fluid can vary depending on the application and the type of machinery it is used in.
Base Oil and Water Content
The base oil used in hydraulic fluid can be either mineral oil-based or synthetic oil-based. Mineral oil-based hydraulic fluids are made from refined crude oil and are the most commonly used type of hydraulic fluid. They are cost-effective and provide good lubrication properties. On the other hand, synthetic oil-based hydraulic fluids are made from chemically synthesized compounds and offer better performance in extreme temperatures and high-pressure applications.
Water is also sometimes added to hydraulic fluid to improve its performance in certain applications. Water glycol hydraulic fluids are used in applications where fire resistance is required, such as in steel mills and foundries.
Additives and Their Functions
Hydraulic fluid contains various additives that improve its performance and protect the machinery it is used in. Anti-wear agents, rust and corrosion inhibitors, and viscosity modifiers are some of the common additives found in hydraulic fluid.
Anti-wear agents reduce the wear and tear on the machinery by forming a protective layer on the metal surfaces. Rust and corrosion inhibitors protect the machinery from rust and corrosion caused by moisture and other contaminants. Viscosity modifiers improve the fluid’s flow properties and prevent it from thinning out at high temperatures.
Synthetic vs Mineral Hydraulic Fluids
Synthetic hydraulic fluids are becoming more popular due to their superior performance in extreme temperatures and high-pressure applications. They also offer better resistance to oxidation and longer service life compared to mineral-based hydraulic fluids.
However, synthetic hydraulic fluids are more expensive than mineral-based hydraulic fluids. The choice between synthetic and mineral-based hydraulic fluids depends on the application and the machinery’s requirements.
Biodegradable Hydraulic Fluid Options
Biodegradable hydraulic fluids are becoming more popular due to their environmental benefits. These fluids are made from renewable resources and are biodegradable, making them a more sustainable option.
There are two types of biodegradable hydraulic fluids: vegetable oil-based and synthetic ester-based. Vegetable oil-based hydraulic fluids are made from natural oils such as rapeseed oil, soybean oil, and sunflower oil. Synthetic ester-based hydraulic fluids are made from chemically synthesized compounds and offer better performance in extreme temperatures.
In summary, hydraulic fluid is a combination of base oil and various additives. The base oil can be either mineral oil-based or synthetic oil-based, and water can be added to improve its performance in certain applications. Additives such as anti-wear agents, rust and corrosion inhibitors, and viscosity modifiers improve the fluid’s performance and protect the machinery it is used in. The choice between synthetic and mineral-based hydraulic fluids depends on the application and the machinery’s requirements, and biodegradable hydraulic fluids offer a more sustainable option.
Properties and Characteristics
Hydraulic fluid is a critical component of hydraulic systems, and its properties and characteristics play a vital role in ensuring the system operates efficiently and effectively. Here are some of the key properties and characteristics of hydraulic fluid:
Viscosity and Viscosity Index
Viscosity is a measure of a fluid’s resistance to flow. In hydraulic systems, viscosity is critical because it affects the system’s ability to transfer power. A hydraulic fluid with low viscosity will flow easily and transfer power efficiently, but it may not provide enough lubrication and wear protection. On the other hand, a hydraulic fluid with high viscosity will provide excellent lubrication and wear protection, but it may not flow efficiently and could reduce the system’s overall performance.
The viscosity index is another important characteristic of hydraulic fluid. It measures the fluid’s ability to maintain its viscosity under varying temperatures. A high viscosity index means the fluid’s viscosity changes less with temperature, which is important in hydraulic systems that operate in extreme temperature conditions.
Lubrication and Wear Protection
Hydraulic fluid also plays a critical role in lubricating the system’s components and protecting them from wear. Without proper lubrication, the metal parts of the hydraulic system would rub against each other, causing damage and reducing the system’s efficiency.
The hydraulic fluid’s lubrication and wear protection properties are determined by the type of base oil used in the fluid. Mineral oils are commonly used as a base oil, but synthetic oils are becoming increasingly popular due to their superior lubrication and wear protection properties.
Corrosion Inhibition and Oxidation Stability
Hydraulic systems are susceptible to corrosion, which can cause damage to the system’s components and reduce its efficiency. Hydraulic fluid can provide corrosion inhibition properties to protect the system from corrosion.
Oxidation stability is another important characteristic of hydraulic fluid. It measures the fluid’s ability to resist oxidation, which can cause the fluid to break down and reduce its effectiveness.
Temperature and Pressure Tolerance
Hydraulic systems can operate in extreme temperature and pressure conditions, and the hydraulic fluid must be able to withstand these conditions. High-temperature hydraulic fluids are designed to operate in extreme temperature conditions, while low-temperature hydraulic fluids are designed to operate in cold temperatures.
The hydraulic fluid’s pressure tolerance is also critical. It must be able to withstand the pressure generated by the system without breaking down or causing damage to the system’s components. High-pressure hydraulic fluids are designed to operate in high-pressure conditions, while low-pressure hydraulic fluids are designed to operate in low-pressure conditions.
In summary, the properties and characteristics of hydraulic fluid are critical to the efficient and effective operation of hydraulic systems. The hydraulic fluid’s viscosity, lubrication and wear protection properties, corrosion inhibition and oxidation stability, and temperature and pressure tolerance must all be carefully considered when selecting the appropriate hydraulic fluid for a particular system.
Hydraulic Fluid in System Performance

Hydraulic fluid is a vital component of a hydraulic system. It plays a crucial role in ensuring the system’s performance, energy transmission, and efficiency. The following subsections will explore how hydraulic fluid affects different parts of the system.
Energy Transmission and Efficiency
Hydraulic fluid is responsible for transmitting energy within the hydraulic system. The fluid’s viscosity and flow rate determine how efficiently it can transmit energy. Higher viscosity fluids are better suited for high-pressure systems, while lower viscosity fluids work better in low-pressure systems. Additionally, the fluid’s flow rate affects the system’s energy efficiency. A higher flow rate can increase the system’s efficiency by reducing energy losses due to friction.
Hydraulic Pumps and Motors
Hydraulic pumps and motors are responsible for converting the hydraulic fluid’s energy into mechanical energy. The fluid’s viscosity and flow rate affect the pumps and motors’ efficiency. Higher viscosity fluids can cause more friction, reducing the pumps and motors’ efficiency. Conversely, lower viscosity fluids can cause cavitation, leading to pump and motor damage.
Seals, Valves, and Hoses
Seals, valves, and hoses are essential components of any hydraulic system. The hydraulic fluid’s properties affect their performance and lifespan. The fluid’s viscosity and chemical composition can affect the seals’ and hoses’ ability to withstand pressure and temperature changes. The fluid’s chemical composition can also affect the valves’ performance, causing them to corrode or deteriorate over time.
Heat Transfer and Cooling
Hydraulic systems generate a lot of heat due to the friction between moving parts. The hydraulic fluid plays a crucial role in heat transfer and cooling within the system. The fluid’s ability to dissipate heat affects the system’s performance and lifespan. Higher viscosity fluids can retain heat, leading to increased wear and tear on the system’s components. Conversely, lower viscosity fluids can reduce the system’s ability to transfer heat, leading to overheating and damage.
In conclusion, hydraulic fluid is a vital component of any hydraulic system. Its properties affect the system’s performance, energy transmission, and efficiency. Understanding how hydraulic fluid affects different parts of the system is crucial to maintaining the system’s optimal performance and lifespan.
Applications of Hydraulic Fluid
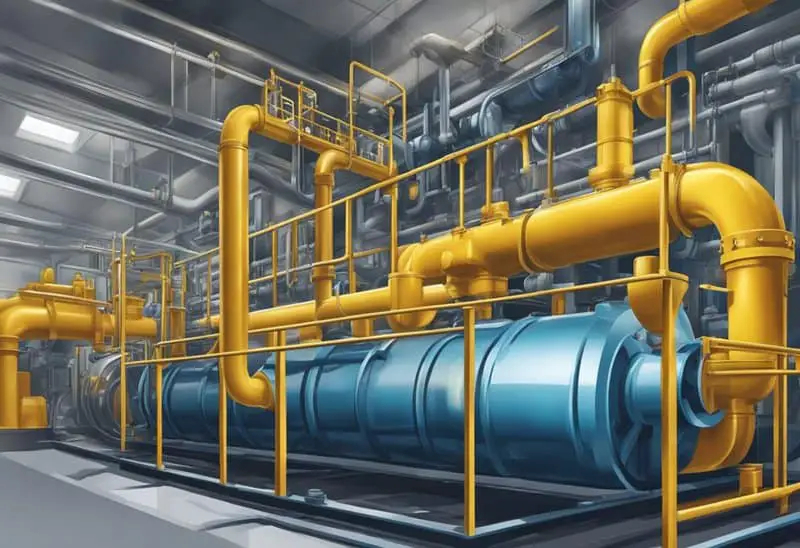
Hydraulic fluid is widely used in various industries and applications due to its unique properties. Here are some of the most common applications of hydraulic fluid:
Industrial and Construction Machinery
Hydraulic fluid is extensively used in industrial and construction machinery such as cranes, excavators, loaders, and bulldozers. These machines require a lot of power to operate, and hydraulic fluid provides the necessary force to move heavy loads and perform various tasks. Hydraulic fluid is also used to lubricate moving parts and prevent wear and tear.
Agricultural and Heavy Equipment
Hydraulic fluid is also used in agricultural and heavy equipment such as tractors, combines, and harvesters. These machines require a lot of power to operate, and hydraulic fluid provides the necessary force to perform various tasks such as plowing, planting, and harvesting. Hydraulic fluid is also used to power the steering and braking systems in these machines.
Aviation and Aerospace
Hydraulic fluid is used in aviation and aerospace applications such as aircraft landing gear, flaps, and brakes. Hydraulic fluid provides the necessary force to operate these systems and ensure safe and efficient operation of the aircraft. Hydraulic fluid is also used in rocket engines and other space applications.
Automotive and Transportation
Hydraulic fluid is used in automotive and transportation applications such as power steering, brakes, and suspension systems. Hydraulic fluid provides the necessary force to operate these systems and ensure safe and efficient operation of the vehicle. Brake fluid is a type of hydraulic fluid that is specifically designed for use in automotive braking systems.
In conclusion, hydraulic fluid is a versatile and essential fluid that is used in a wide range of applications. Its unique properties make it ideal for powering heavy machinery and equipment, as well as providing the necessary force for aviation, aerospace, automotive, and transportation systems.
Maintenance and Safety Considerations
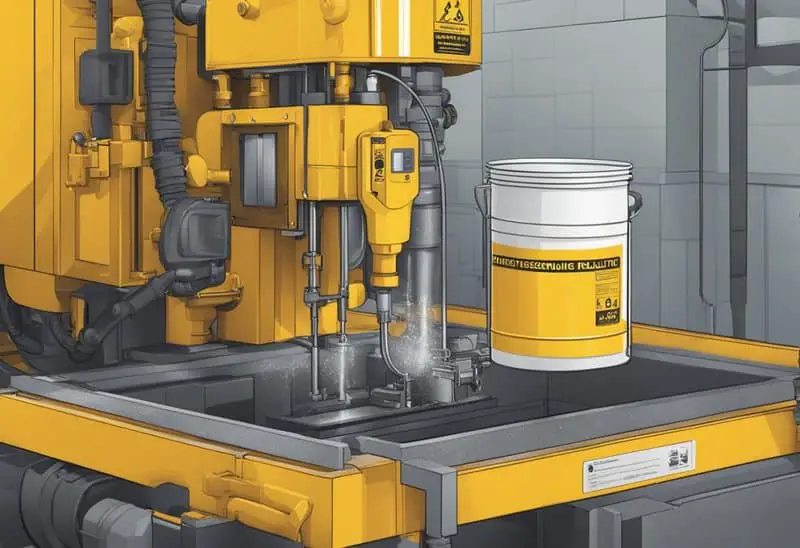
Handling and Storage
Proper handling and storage of hydraulic fluid are critical to ensure its quality and performance. Hydraulic fluid should be stored in a clean, dry, and cool place, away from direct sunlight and sources of heat. It is also essential to make sure that the container is tightly sealed to prevent contamination and moisture absorption.
Before using hydraulic fluid, it is crucial to check its expiration date and make sure that it is still within the recommended shelf life. If the fluid has been stored for an extended period, it is advisable to test its properties before use.
Contamination and Filtration
Hydraulic contamination is a significant concern that can lead to system failure and costly repairs. It is essential to prevent contamination by using proper filtration and maintenance practices.
Filters are critical components in hydraulic systems that remove contaminants such as dirt, debris, and metal particles. It is essential to choose the right filter for the system and replace it regularly to ensure its effectiveness.
In addition to filtration, regular maintenance practices such as fluid analysis and system flushing can help prevent contamination and ensure system performance.
Environmental Impact and Disposal
Hydraulic fluid can have a significant impact on the environment if not handled and disposed of properly. It is essential to follow local regulations and guidelines for the disposal of hydraulic fluid.
Hydraulic fluid should never be disposed of in the environment, such as soil, waterways, or sewers. Instead, it should be collected and disposed of at a licensed waste facility.
In addition to proper disposal, it is essential to consider the environmental impact of hydraulic fluid during its use. Choosing environmentally friendly hydraulic fluids can help reduce the impact on the environment while maintaining system performance.
Overall, proper maintenance and safety practices are critical to ensure the performance and longevity of hydraulic systems. By following proper handling, filtration, and disposal practices, hydraulic fluid can be a reliable and safe component in many industrial applications.
Frequently Asked Questions
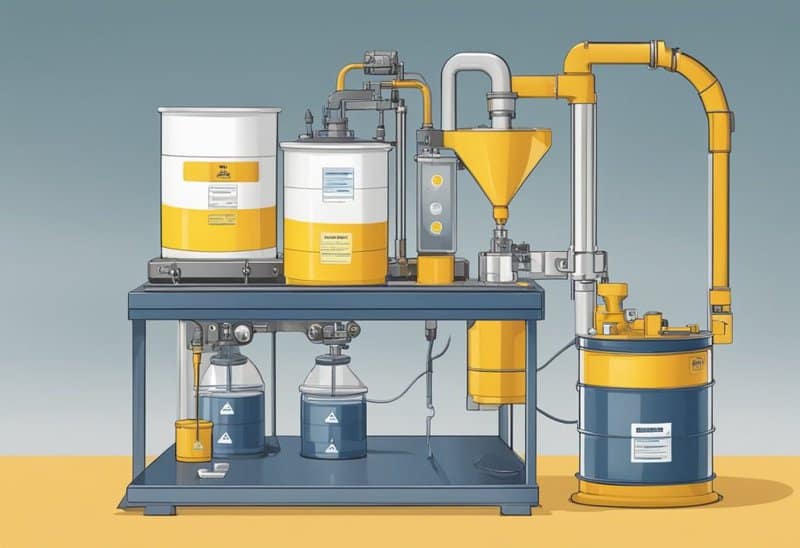
What are the common base oils used in hydraulic fluids?
The most common base oils used in hydraulic fluids are mineral oils, which are derived from crude oil and are the most cost-effective option. Synthetic oils, on the other hand, are made through chemical synthesis and are often used in high-performance applications due to their superior properties.
How does synthetic hydraulic fluid differ from mineral-based varieties?
Synthetic hydraulic fluids are typically more expensive than mineral-based varieties, but they offer better performance in extreme temperatures and under high pressure conditions. They also have a longer lifespan and are more resistant to oxidation and breakdown.
What are the typical additives found in hydraulic oil?
Common additives found in hydraulic oil include anti-wear agents, viscosity improvers, detergents, and rust inhibitors. Anti-wear agents reduce friction and wear between metal surfaces, while viscosity improvers help the oil maintain its viscosity over a wide range of temperatures.
Can you list the four main types of hydraulic fluid?
The four main types of hydraulic fluid are mineral oil-based, water-based, synthetic-based, and bio-based. Mineral oil-based fluids are the most common and are suitable for most hydraulic applications. Water-based fluids are used in applications where fire resistance is required. Synthetic-based fluids are used in high-performance applications, while bio-based fluids are made from renewable resources and are environmentally friendly.
For what purposes is hydraulic oil primarily used?
Hydraulic oil is primarily used to transfer power in hydraulic systems, such as those found in heavy equipment, construction machinery, and vehicles. It is also used to lubricate moving parts and to dissipate heat.
What are the standard grading systems for hydraulic oil?
The most common grading system for hydraulic oil is the ISO viscosity classification system, which assigns a number to the oil based on its viscosity at 40°C and 100°C. Other grading systems include the SAE system, which is used primarily in North America, and the AGMA system, which is used in the United States for industrial gear oils.