Oil seals are probably not given much thought until they begin to leak or entirely stop working. But these little rubber seals are important. They keep liquids in the right place and prevent things from getting ruined. Early oil seal defects usually mean an underlying problem that needs to be fixed to prevent further damage and expensive repairs.
Take a few minutes to learn about some oil seal damage reasons and what you can do to prevent problems in the first place. Taking care of these things from the beginning will make your seals last longer and keep your equipment working well. A little knowledge and preventive action can go a long way.
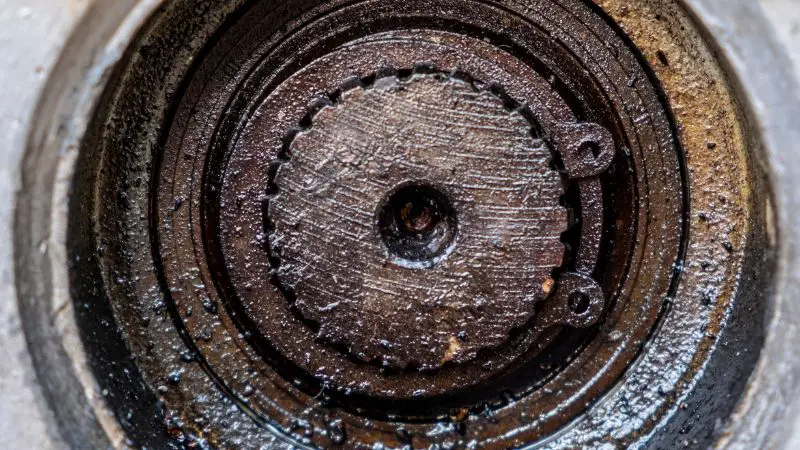
1. Improper Installation: The Most Common Cause of Oil Seal Damage
One of the most common causes of oil seal failure is improper installation. If you don’t install oil seals correctly the first time, they won’t last long, and you’ll be stuck fixing the problem again soon.
To install oil seals properly, first, make sure you have the right seal for the job. Ensure that the diameter, width, and material are suitable for your application. If the seal is wrong, it won’t seal properly and will fail quickly.
Thoroughly clean the area where the seal will be installed. If you leave dirt or stuff behind, the seal won’t fit right or might get scratched when you put it in.
Apply a light coat of oil to the seal before installing it. This helps the seal slide into place without damage. Once the seal is installed, wipe away any excess oil. Too much oil left behind could attract dirt and grit, damaging the seal over time.
When installing the seal, gently tap it into place using a socket or installation tool. Never force an oil seal into place, as this can cause damage. Take your time and make sure the seal is going in evenly.
After installation, double-check that the seal is evenly seated, and flush with the surface it’s meant to seal. If it’s crooked or damaged, remove it and start over. It’s worth taking a few extra minutes to get it right the first time.
2. Excessive Heat
Excessive heat can do a number on oil seals. High temperatures cause the seal material to break down faster, leading to cracks, leaks, and premature failure.
- The hotter it is, the softer and more pliable the seal becomes, allowing more particles to get in and wreak havoc. At extreme temps, the seal can harden and become brittle.
- Higher heat also accelerates chemical reactions that degrade the seal. Oxidation in particular causes the seal to stiffen, shrink, and crack.
- The internal lubricants and plasticizers that keep seals flexible start to evaporate at high heat. Without these, the seal loses elasticity and can no longer seal properly.
To avoid overheating oil seals, make sure any equipment they’re used in has adequate cooling and ventilation. Keep operational temperatures within the recommended range for your specific seals. It may also help to choose high-temperature seal materials, like fluorocarbon rubber, that can handle more extreme conditions.
There could be various causes of seal failure in food packaging such as improper maintenance and improper storage. Regular maintenance is essential to prevent oil seal damage.
3. Chemical Exposure
Oil seals may sustain damage from chemical exposure, compromising their integrity and reducing their lifespan. Some substances have the potential to weaken, swell, shrink, or otherwise harm the seal material. Take steps to prevent exposure to any chemicals that may meet oil seals.
Corrosive chemicals
Oil seals can become damaged by strong acids and alkalis, which degrade the seal and weaken the substance. Eventually, damage can be done by even water-based solutions. If oil seals are exposed to chemicals like sodium hydroxide (lye), hydrochloric acid, or sulfuric acid, then they should be checked frequently.
Solvents
Acetone, lacquer thinner, and toluene are organic solvents that can dissolve or expand seal materials like silicone or nitrile.
Oxidizing agents
Chemicals like hydrogen peroxide, chlorine, and ozone can oxidize oil-seal materials, making them brittle and prone to cracking.
Plasticizers
Phthalate plasticizers that soften PVC can migrate into nitrile or neoprene seals, causing them to swell, soften, and lose shape.
4. Excessive Wear
Excessive wear is one of the top reasons for oil seal defects. To ensure your oil seals provide long-lasting performance, it’s important to understand what can cause premature wear and how to prevent it.
Mechanical Seal Damage Reasons and Failure Analysis
Oil seals are an essential component of many kinds of machinery and equipment, playing a vital role in preventing leaks and maintaining optimal performance. However, like any other mechanical part, oil seals are subject to wear and tear over time, and a variety of factors can shorten their lifespan.
In the previous section, we discussed how exposure to chemicals can compromise oil seal integrity and lead to damage and failure. In this section, we will explore some other common mechanical seal damage reasons and analysis of them.
Temperature and Pressure
Temperature and pressure are two of the most significant factors that can impact oil seal performance. High temperatures can cause seal materials to become brittle, crack, or lose their shape, while excessive pressure can lead to seal deformation or failure.
Check: What Is The Ideal Oil Temperature?
Shaft Misalignment: How Improper Alignment Can Cause Oil Seal Defects
Shaft misalignment is another factor that can contribute to pump seal failure and damage. When the shaft is not correctly aligned with the seal, it can cause the seal to wear unevenly, leading to leaks and other issues. These are a few tips to avoid shaft misalignment:
- Use precision alignment tools and techniques to ensure that the shaft is aligned correctly with the seal.
- Make sure that the shaft is not bent or warped, as this can also cause misalignment.
- Avoid excessive vibration or shock that could cause the shaft to move out of alignment.
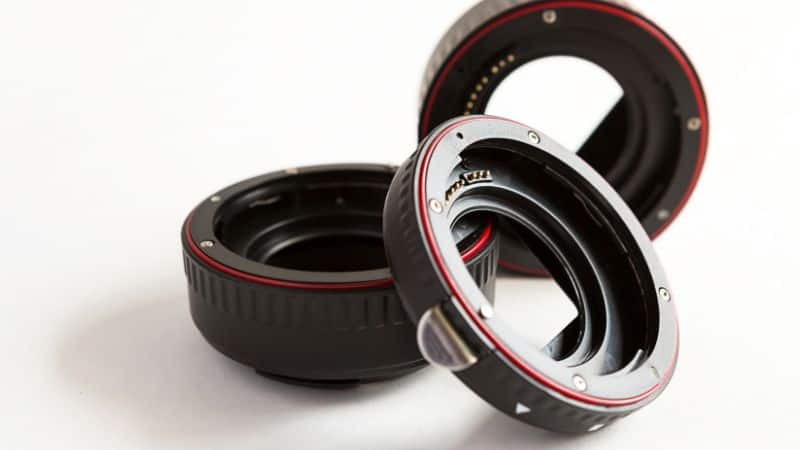
Prevention of Oil Seal Damage
Oil seal selection & maintenance both are very important in your engine service life because worn or wrong oil seal can’t work as a proper sealant. Let’s look into some necessary issues:
Choose the Right Seal for the Job
Selecting oil seals made of materials compatible with the fluids and temperatures they’ll be exposed to is key. Common seal materials include nitrile (for hydraulic fluids), silicone (for high heat), and fluorocarbon (for aggressive chemicals). Choose a seal with the highest temperature and chemical resistance possible for your application.
Maintain Proper Seal Lubrication
Most seals require some lubrication to prevent overheating and wear. For rotating shafts, use the appropriate oil specified for your equipment. For reciprocating shafts, compatible grease may be needed. Without lubrication, seals can deteriorate rapidly. Be sure to lubricate seals during installation and periodically inspect them to ensure proper lubrication and cooling.
Limit Contaminants
Contaminants like dirt, dust, or metal chips can get caught between the seal lip and shaft, causing abrasive wear. Install seals in clean housing and seal any gaps or holes where contaminants might enter. Periodically inspect seals for built-up debris and clean or replace them as needed.
Control Seal Environments
Excessive heat can cause seals to harden and wear prematurely. Most seals have a maximum temperature rating that should not be exceeded. Similarly, extremely cold temperatures can cause seals to become brittle. Maintain seal environments within the recommended temperature range for optimal performance and longevity.
Inspect and Replace Seals Regularly
Over time, seals will naturally experience some wear and their performance will start to deteriorate. Most seals should be inspected periodically based on the severity of the application. Look for signs of wear like torn, cracked, or damaged seal lips, as well as fluid leakage. Replace any seals before they completely fail to prevent costly damage or downtime.
Frequently Asked Questions
Question: Do oil seals wear out over time?
Answer: Yes, oil seals can wear out over time.
Question: How long should oil seals last?
Answer: The lifespan of oil seals can vary depending on factors such as usage, maintenance, and operating conditions, but they typically last for several years.
Question: How can we prevent mechanical seal failure?
Answer: To prevent mechanical seal problems, remember to use enough oil, keep things from getting too hot or squished, keep everything clean, and check for worn-out seals often.
Wrapping Up
Your oil seals can provide years of reliable performance with proper selection, installation, lubrication, and maintenance. Paying attention to these factors will help maximize their service life and ensure the smooth, efficient operation of your equipment.