The punching oils can act as highly mechanically and thermally stable liquids. With a high-pressure resistance, these oils are accessible and enable sufficient element flow. Oil can remove the tool wear. They are formulated to meet the requirements of the punching process. Besides this, they are accessible with progressive separating and wetting characteristics.
Also, they are suitable for fine-cutting work and are used with high alloy steels. Additionally, without lubrication, the dies of this oil are necessary for lubrication and punching of other metal objects. Mainly, you can serve this oil as a rust inhibitor in steel. Actually, they are non-toxic and allow for maximum effectiveness. Let’s talk more about punching oil.
What Is Punching Oil?
Punching oils comes to fulfill your particular technical and performance requirements. In addition, it can provide lubricity during operation—no sulfur or chlorine-containing products that can cause corrosion problems. You can use this punching oil in light stainless steel, aluminum, and mild steel.
You can use this product by dipping, brushing, dripping, or wiping. The flush point of this punching oil is 130°F which can prevent buildup on rollers. With this product, you can perfectly clean your tool and improve your tool life. Fortunately, this oil contains rust preventive and extreme pressure additives to ensure excellent performance.
What Is The Application Of Punching?
Punching is a separating method, mainly used to process holes into flat tools like paper, sheet metals, or plastic film. Typically, the punching component has two tool parts – one support for the dies and one for the punches. Mainly, you can use this punching to process the circular or profile holes in the flat element. But this is perfect for applications where garbage removal may cause issues.
In the last few years, punching has become crucial for metal foil processing for technologically sophisticated products. For example, in the aerospace or electronics industries. Another application is punching profiles into metal sheets and building industries.
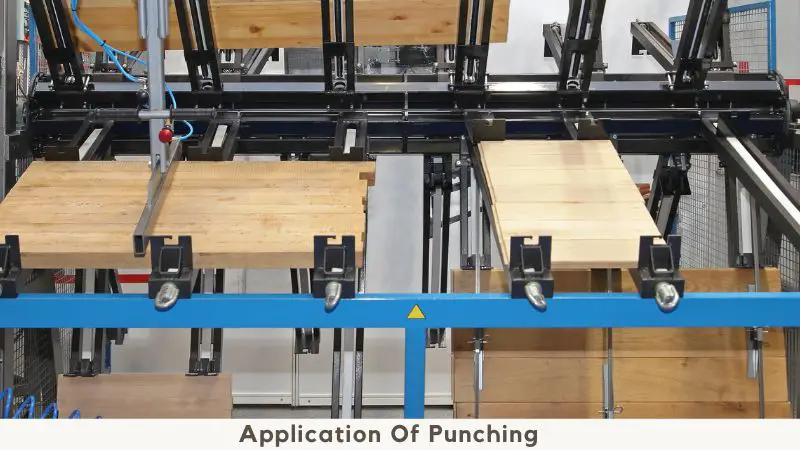
What Is Punching In The Manufacturing Process?
This forming process uses a punch press called a punch to force a tool. Through the workpiece, it creates a hole by shearing. You can apply this process to many materials that come in sheet form. For example, they are applicable in paper, sheet metal, plastic sheets, and vulcanized fiber.
Punches often pass through the work in a die. In the process, scrap slag from the hole is deposited on the die. Depending on the punched element, this slug can be reused or discarded.
Punching is almost the cheapest process for making holes in sheet elements in medium to high production quantities. The process is called blanking when a specifically shaped punch is applied to create many usable parts.
Process
Punch tooling is almost manufactured of tungsten carbide. You can find the die on the opposite side of the workpiece and support the element around the hole. Yet, it helps localize the shearing force for a cleaner edge.
Because of some clearance between the punch and the die, this punch doesn’t get stuck in the die. For that reason, it can get less force to make the hole. The clearance amount depends on thickness, and thick elements need extra clearance.
But it always happens that the release is less than the workpiece thickness. Through a workpiece, the punch press forces the punch to make a hole, and the diameter is the same as the punch.
When punched, all flexible tools extend, almost resulting in the punch sticking in the workpiece. In this case, you must physically pull the punch out of the hole if the work is supported. This entire process is known as stripping.
What Different Punching Processes Exist?
You can generally find two different punching processes, conventional flat-bed punching, and rotary punching. We have described these two processes in detail below.
Flat-bed Punching
A flat-bed punching unit has a press with an integrated punching tool. Punching tools usually have an upper and a lower tool. These tools are mounted parallel to the linear guides and are precisely adjusted. Because of it, the punches can enter the dies correctly. The component web is performed in vertically moving tools.
When the punches enter the die, the entire punching pressure works on the element simultaneously. The punched garbage is pushed into the dies and falls vertically down.
Rotary Punching
A rotary punching unit punching tools are mounted directly on highly accurate bearings or adjustable on two cylinders. The substance’s web constantly moves between two rotating devices. Relying on the application, the complete punching unit can be integrated into one machine frame.
Continually the tools rotate during punching. Thus, the punch enters the die in sequence. The timely force needs less punching force than flat-bed punching. You can eliminate the garbage with a hollow die cylinder.
Diacut NCL Oil:
Accordingly, this is high-quality, fully synthetic cutting oil. And it’s best for milling, cutting, and drilling all FE and NE metals. In particular, it provides very exceptional corrosion and wear protection. Usually, it’s best to use for high cutting speeds and long service life.
What Oil Is Best For Oiling Tools?
Lubricant oil comes with many purposes, especially regarding machinery and equipment. Industrial workers use lubricants to prevent gears and other parts from grinding in machinery. Automobile owners apply lubricants to their car parts for the same reason.
Furthermore, you can use oil on printers, firearms, and sewing machines. All types of people depend on beat lubricant. That’s why they always search and invest in the best oil. However, let’s know the best oil for your oiling tools:
- Lucas Oil Air Tool Lubricant Oil
- WD-40 Multi-Use Lubricant Oil
- 3-IN-ONE Multi-Purpose Lubricant Oil
- Trick Shot Penetrating Lubricant Oil
Final Word:
In short, you need to use punching oil for your punching process. But from a wide range of punching oil, you should use the best one. Ultimately, they need to manufacture bending and stamping parts and more.
Nevertheless, here we are trying to give valuable information about punching oil. All of this information will be helpful for you. Though there is little information about this topic, we are trying to give accurate information for you. Thanks for reading this article.
Read About: Quenching Oil