Hydraulic oil works as an energy transfer medium in the working process of a hydraulic system. The hydraulic oil performance directly impacts the condition and efficiency of the transmission. The foaming of hydraulic oil is a crucial aspect that endangers the hydraulic system’s regular operation.
Additionally, if not addressed, this can cause problems affecting your final drive motor. In this case, you need to use anti-foaming hydraulic oil on your hydraulic system. It’s because antifoam agents can inhibit foam formation and act as a defoamer to break down any existing foam. However, let’s learn what anti-foam is and the jobs of anti-foaming hydraulic oil in detail.
What Are Anti-foams?
Anti-foams are additives that prevent foam formation. Yet, anti-foams can stop foam interference and damage. Besides this, it allows peak performance of your hydraulic system. Silicone and polypropylene glycols are effective alternatives as anti-foams.
In other words, anti-foam additives are polysiloxane-based compounds utilized in multipurpose additive packages. For example, you can use them in detergents, medicines, and process industries. Some common additives are insoluble oils and other silicones, certain alcohols, stearates, polydimethylsiloxane, and glycols. The other name of an anti-foam additive is a defoamer or foam inhibitor.
Anti-foam additives can also prevent foam formation or break the already-formed foam. It also reduces the fuel spillage possibility on the ground or clothing and avoids staining and unpleasant odor nuisances. Even so, it can reduce the risk of spills contaminating the soil and atmosphere. Likewise, they are common in many lubricating oils and hydraulic oils.
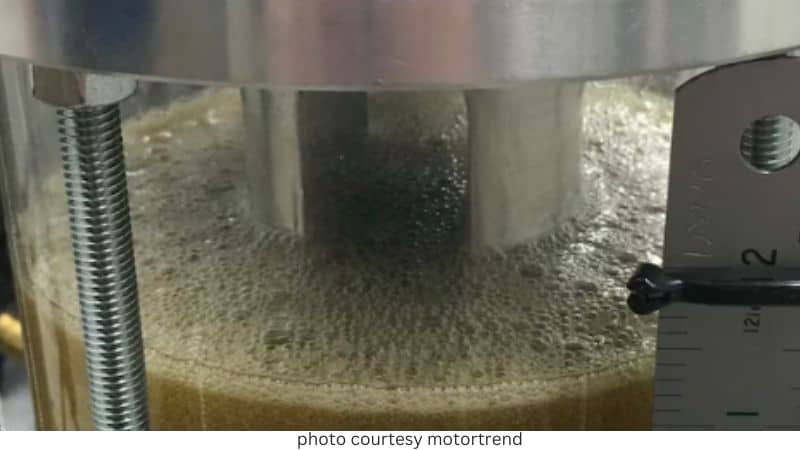
What Is Anti-Foaming Hydraulic Oil?
When you use hydraulic oil, many contaminants may enter the hydraulic system because of working conditions. These contaminants can be roughly divided into machine parts, external penetrating, and reproducible pollutants. From these pollutants, some are responsible for expanding the foaming of hydraulic oil.
Foaming can disrupt your system’s central refinery process units, decrease run time, and degrade sensitive equipment operations. Foam air bubbles cause a variety of problems in oil. These make it difficult to pump oil to critical engine parts, reducing the lubrication effectiveness of the oil. Similarly, foamy oil will inhibit the oil’s ability to keep the engine cool even if it causes severe engine damage.
Anti-foam additives effectively eliminate these concerns. It works by decreasing the surface tension of the air bubble walls that form the foam, causing it to collapse faster. Adding anti-foaming agents in hydraulic oil can prevent these problems, especially at high temperatures. Foaming not only increases oil oxidation but also reduces lubrication effects. Only anti-foaming hydraulic oil can reduce this problem.
Benefits Of Anti-foaming Hydraulic Oil:
- Great anti-wear performance
- Effectively reduce hydraulic pump wear
- Extending the service life of pumps and hydraulic systems.
- Adequate oxidation stability
- Good anti-rust and anti-corrosion performance
- Effectively prevent oil from leaking.
- Useful demulsibility performance
- Excellent anti-foaming performance
Anti-foaming Agents For Hydraulic Oil:
Anti-foaming agents are generally divided into three types used in hydraulic oils. There are non-silicone, silicone, and compound types. The defoaming effect of silicone antifoaming agents is better than non-silicone anti-foaming agents. When adding an anti-foaming agent to hydraulic oil, you should consider the impact of the hydraulic air release performance.
Studies have shown that adding silicone antifoaming agents can worsen the hydraulic oil air release performance. Non-silicone and composite anti-foaming agents have little impact on the air release performance. Thus, consider using non-silicone or compound anti-foaming agents if hydraulic oil products release poor Air.
When choosing anti-foaming agents, consider failing agent compatibility and other additives. It’s because silicone has better compatibility with different additives. But, using non-silicone agents with three additives, T601, T109, and T705 combinations, can promote oil foaming.
Why Is My Hydraulic Oil Foaming?
Is foaming hydraulic oil a big concern or a minor problem? You may want to know about this. Well, if you ignore tractor hydraulic oil foaming, it can cause severe problems with your final drive. Though foaming is a common problem, you can also find many solutions. Some of the leading causes of hydraulic oil foaming are as follows:
Air Entrapment:
Air entrapment can happen during hydraulic system operation, filling, or maintenance. Subsequently, Air can get trapped in the oil, creating bubbles that cause foaming.
Contamination:
Pollutants like water, dirt, and other impurities can cause foaming in hydraulic oil.
High Velocities:
High velocities can cause oil to aerate and form foam. Basically, this can happen in high-flow components like valves and pumps and high-pressure.
High Temperatures:
High temperatures can cause oil to become more volatile and foam. Particularly, this is problematic in systems that work at high temperatures, like in heavy-duty components.
Chemical Incompatibility:
Using incompatible hydraulic oil with system components and seals may cause foaming. If you have already used a defoamer, foaming may occur if you use too much or if it runs low.
Anti-Foaming Hydraulic Oil Substitute
Read on if you want to know what an anti-foaming hydraulic oil substitute is. Nevertheless, you can use a replacement if you need to use another oil instead of anti-foaming hydraulic oil. You can use an alternative as an anti-foaming hydraulic oil in an emergency. So, in the place of anti-foaming hydraulic oil, you can use vegetable oil. Moreover, you can use mineral oil temporarily.
Mainly, you should need to check the compatibility before using it. After driving a few miles, you should change this oil immediately. Most microbes do not metabolize mineral oil. Similarly, you also can use plant oil as an alternative to anti-foaming hydraulic oil. You can use it if you are limited by cost or if silicone-based reagents have too many toxic side effects.
Nonetheless, some commonly used anti-foaming agent substitutes are:
- Cetostearyl alcohol
- Castor oil
- Stearates
- ethers
- Other silicone derivatives
- glycols
Best Anti-Foaming Hydraulic Oil
Are you looking for the best anti-foaming hydraulic oil to remove foaming? We have furnished some of the best anti-foaming hydraulic oils here. Have a look:
ZP-900 Hydraulic Anti-Foam:
ZP-900 Hydraulic anti-foam has wet anti-wear lubricants, oxidation inhibitors, pour point depressants, viscosity index enhancers, and foam-reducing agents. The formula of ZP-900 doesn’t decrease the lubricating ability of the fluid like silicone defoamers. Yet, it reduces most common hydraulic system problems like wear, corrosion, leakage, and cavitation.
Making a barrier between metal-to-metal contact develops the load-carrying system capacity and reduces pump strain and friction. In addition, it also decreases frictional warmth build-up, which decreases varnish, oxidation, sludge, and acid. Furthermore, using this oil can release the valve, and your hydraulic oil will last longer.
Using anti-foaming agents, ZP-900 prevents disastrous pump cavitation and energy loss when air bubbles form in hydraulic systems. Usually, ZP-900 decreases heat load and prevents oil solution; it adds a viscosity index improver. At or below 120°F, oil oxidizes very slowly. Above 135°F, the oxidation rate doubles for every 18° rise in temperature. The ZP-900 is compatible with all standard hydraulic systems.
Non-Foaming Hydraulic Fluid Napa:
Napa non-foaming hydraulic fluid is a Premium HD Hydraulic fluid. This Multi-viscosity 10w20 fluid feature is suitable for year-round use. It provides non-foaming and outstanding anti-wear protection. Also, it offers extreme pressure protection for your highly loaded gears.
Hence, it meets the OE-approved formulation and additive system. Accordingly, you can use this NAPA non-foaming hydraulic oil in your Caterpillar TO-2, Renk Bus ATF, Eaton hydraulics, etc.
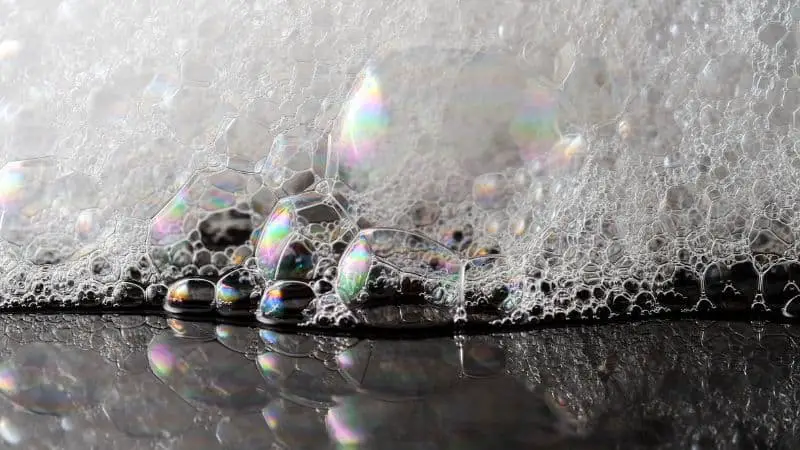
FAQ (Frequently Asked Questions)
Q. How do you stop hydraulic oil from foaming?
Add an anti-foaming agent to the hydraulic oil to combat the appearance of foam. Actually, Anti-foaming agents contain esters or silicone oils. They spread on the liquid surface and foam. Over time, they can remove the bubbles and release the trapped Air.
Even so, you can stop foaming by using high-quality hydraulic oil, which is suitable for the system. Always maintain your system according to your manufacturer’s instructions and keep your system contaminate-free. In particular, always monitor the system for signs of foaming and address the problem immediately.
Q. What is non-foaming hydraulic oil?
Non-foaming hydraulic oil is an anti-wear, zink-containing hydraulic oil. In particular, this hydraulic oil provides excellent protection against rust, corrosion, wear, foaming, and thermal breakdown. In fact, it has terrific water separation and filterability properties.
Final Word:
Hydraulic oil foaming is a common problem in hydraulic systems that can reduce performance and increase wear on elements. Accelerated aging of hydraulic fluid, spongy operation, and cavitation corrosion can result from unwanted hydraulic foaming.
In particular, if you use anti-foaming hydraulic oil, you can solve all these issues immediately. When you use hydraulic oil, you should check the anti-foaming performance of hydraulic oil regularly. If hydraulic oil’s anti-foaming performance is poor, use a certain amount of anti-foaming agent. Thanks for reading this article.
Now Read About Eco-Safe Hydraulic Oil