The oil is important for the equipment that helps keep the equipment going and running well. You want to be sure that you have enough oil in the tank so that the compressor can run well.
There are a lot of things to know about when it comes to the oil in an air compressor tank. You want to be sure that you are adding the right kind of oil, and you also want to be sure that you are adding enough of it. Check out this article and know an overall idea of oil in an air composer tank.
What is Oil in an Air Compressor Tank?
An air compressor tank collects the compressed air from the compressor’s pump. The compressed air is at very high pressure and is either stored in the tank or sent directly to the pneumatic tools through a pipe. The air compressor tank must be large enough to store the entire volume of compressed air that is produced by the pump during each cycle.
The compressed air is usually at a pressure of between 150 and 300 psi, but it can be as high as 1,000 psi. The oil in the air compressor tank helps keep the compressed air cool and lubricates the compressor’s pump.
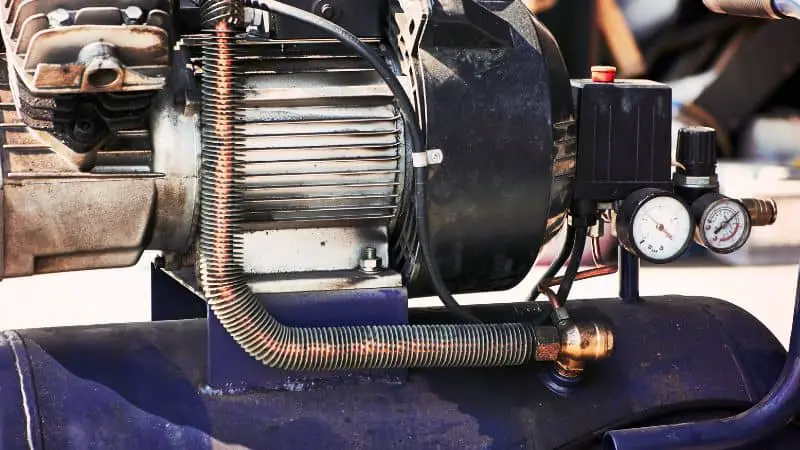
Types of Oil Used in Air Compressor Tanks
There are two main types of oil used in air compressor tanks: mineral oil and synthetic oil. Both have their benefits and drawbacks, so it’s important to understand their differences before making a decision.
Mineral oil is a natural substance that’s derived from crude oil. It’s a common lubricant for machinery because it’s affordable and easy to find. However, it can be difficult to biodegrade, which means it can damage the environment if it’s not disposed of properly.
On the other hand, Synthetic oil is made from man-made materials. It’s more expensive than mineral oil but also more environmentally friendly because it degrades easily. Also, synthetic oil is less prone to forming harmful deposits, which can cause problems with the compressor over time.
What are the reasons for oil carryover in air compressors?
Oil carryover in air compressors is a common issue. It is caused when lubricant oil used in the compressor is mixed with the air during compression, resulting in a visible mist and oil droplets in the compressed air stream. There are several reasons why oil may carry over in an air compressor:
Worn or damaged piston rings or cylinder walls
These components are responsible for maintaining a tight seal between the compression chamber and the crankcase, which can prevent oil from entering the compressed air stream. If these parts are worn or damaged, the oil may be able to leak into the compressed air.
Clogged air filters
If the air filters on the compressor become clogged with debris, they can restrict the airflow and cause the compressor to work harder than it should. This can lead to increased oil carry-over.
High oil levels in the crankcase
If the oil level in the crankcase is too high, it may be forced into the compression chamber during operation, leading to oil carry-over.
High-pressure operation
Compressors that are operated at high pressures are more susceptible to oil carry-over than those operated at lower pressures. This is due to the increased force exerted on the cylinder walls and piston rings, which can cause more oil to be forced into the compressed air stream.
Poor maintenance practices
If maintenance is not performed on the compressor on schedule can also cause oil carry-over by not replacing the oil filter and air filter, oil leakages and not keeping the compressor clean.
It is important to regularly check the oil level, and keep an eye out for any unusual odors or discoloration in the compressed air. If oil carry-over is detected, it should be addressed immediately to prevent damage to downstream equipment and to ensure the quality of the compressed air.
Causes of Oil Carryover in Screw Compressors
There can be several reasons why oil might carry over from a screw compressor into the downstream piping and process. It’s important to understand these causes so that you can take steps to prevent or minimize oil carryover.
Some of the most common causes of oil carryover include:
• Dirty or damaged compressor seals
• Improperly adjusted or maintained valves and seals
• Incorrect piping arrangements or fluid velocities
• Foreign material (e.g. dirt, dust, rust) in the compressor discharge
Common Signs of Failing Oil in Air Compressor Tanks
It’s important to know the signs of failing oil in your air compressor tank so you can take appropriate action. If you notice any of the following, it may be a sign you need to check your oil:
Low oil level:
One of the most obvious signs of failing oil is a low oil level. This can be caused by a leak or simply by the oil breaking down and becoming less effective. If the oil level is low, it’s important to add more oil and check for leaks.
Dark or dirty oil:
The oil in your compressor should be clean and transparent. If the oil appears dark or dirty, it may be contaminated and should be drained and replaced. This could be caused by impurities in the air or by the presence of water, which can cause the oil to deteriorate.
Strange noises:
Air compressors can be quite loud, but if you notice strange or unusual noises coming from the machine, it may be a sign that the oil is failing. This could be caused by a lack of lubrication, which can lead to increased friction between moving parts, resulting in increased noise
Reduced performance:
If the compressor is not running as efficiently as it should be or if it’s not reaching the desired pressure, it may be a sign that the oil is failing. This could be caused by a lack of lubrication or by the oil breaking down and becoming less effective.
Overheating:
If the oil is not properly lubricating the compressor, it could lead to overheating, which can cause damage to the machine.
It’s very important to keep an eye out for these signs and to regularly inspect your system for any kind of oil leakage. If you catch a problem early enough, it can save you time and money in the long run. Plus, taking care of your oil is essential for safe and efficient operation and performance.
How to Repair Excess Oil Carryover in Screw Compressors
There are a few ways that you can repair excess oil carryover in screw compressors. The first thing you can do is increase the compressor’s suction pressure. This will help to pull more oil out of the system.
You can also try cleaning the compressor’s suction filters more often. This will help to remove any impurities that may be causing the oil to carry over.
Also, try flushing the system with a solvent. This will help to dissolve any of the oil that has built up in the system and is causing the carryover. Be sure to consult with your compressor manufacturer to find out which solvents are compatible with your machine.
And finally; you can also try adjusting the compressor’s operating parameters. This includes adjusting the compressor’s inlet temperature and pressure, as well as its speed. Be sure to make these adjustments gradually, so you don’t overload the system and cause additional problems.
Frequently Asked Questions
Q. If oil gets into the air supply line from the compressor what kind of defects could this cause?
If oil gets into the air supply line from the compressor, it can cause a variety of defects. The most common defects include a decrease in power output, reduced fuel efficiency, increased emissions, and increased wear and tear on the engine. In extreme cases, the oil may even cause engine failure.
Q. Why is there oil in my air compressor tank?
The oil in your air compressor’s tank is there to lubricate the moving parts of the compressor and help keep it running smoothly. Without the oil, the components inside the compressor would eventually grind against each other, leading to excessive wear and tear, and premature failure.
Q. How to clean oil out of the air compressor tank?
The best way to clean oil out of an air compressor tank is to drain the tank and follow up with a thorough cleaning. First, drain the tank and dispose of the oil properly. Next, use a brush and mild detergent to scrub the inside of the tank to remove any residual oil and dirt. Lastly, rinse the tank with clean water and allow it to air dry.
Conclusion
The main reason compressor oil degrades and breaks down is because of air oxidation. Air contains a high level of oxygen which, when combined with the hydrocarbons in the compressor oil, creates a degradation process that results in the formation of sludge and varnish.
Read Also: Rotary Screw Compressor Oil